CFOAM® Carbon Foam Catalytic Converter Applications

ADVANCES IN CATALYTIC CONVERTERS AND EMISSION SYSTEMS HAVE REDUCED EMISSIONS BY MORE THAN 95% FROM THE UNCONTROLLED PERIOD OF THE 1960’S.

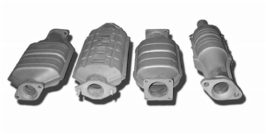
In order for a catalytic converter to perform efficiently, it must allow for the exhaust gases to pass in close proximity to the catalytic materials on the substrate’s surface, and at same time the element must create a low restriction in the flow of exhaust gases.
Furthermore, as emission restrictions tighten even more, increasing emphasis is being placed on the time it takes to bring a catalytic converter to operating temperature, during which time 60%-80% of all non-methane hydrocarbons (NMHC) and carbon monoxide (CO) emissions occur.
CFOAM® carbon foam’s open cell structure presents an ideal high surface area catalyst substrate in which the flow path through the foam creates a mixing effect to the exhaust stream. This mixing effect increases exposure of the exhaust gases to the catalysts and can increase the efficiency of the converter.
By controlling the electrical resistivity of the carbon foam substrate and applying current to the catalyst element, the entire substrate can act as an electric heating element and shorten the time required to reach operational temperatures. Through variations of thermal properties, CFOAM® carbon foam can also be designed as the shell that houses the catalyst elements.